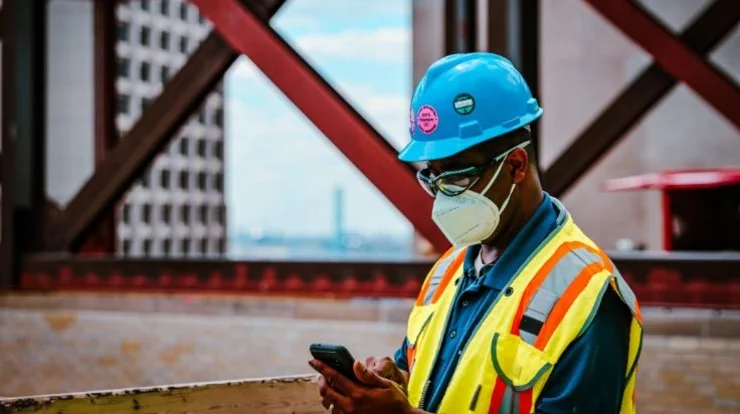
Welcome to the comprehensive guide on acing your industrial safety interview! In the world of industrial safety, being prepared isn’t just a motto; it’s a necessity. This blog post is your trusty companion, equipping you with a trove of frequently asked questions and sharp, insightful answers that will help you navigate the often-challenging terrain of industrial safety interviews. Whether you’re a seasoned safety professional or a newcomer to the field, these questions cover a spectrum of scenarios – from operational and situational dilemmas to behavioural challenges – ensuring you walk into your interview armed with knowledge, confidence, and a dash of finesse.
Frequently Asked Questions
1. What are the key components of an effective industrial safety program?
- Answer: The key components include risk assessment, safety training, emergency preparedness, compliance with regulations, accident investigation, and continuous improvement. It’s about creating a culture of safety that involves everyone in the organization.
2. How do you stay updated with industrial safety regulations and best practices?
- Answer: I regularly attend industry workshops and seminars, subscribe to safety publications, and participate in relevant online forums. Staying connected with professional safety organizations also helps in keeping up-to-date with changes in regulations.
3. Can you describe a time when you improved safety at a workplace?
- Answer: In my previous role, I identified a recurring issue with machinery safety. I led a team to implement enhanced safety measures, including additional guards and improved training for operators. This resulted in a 40% reduction in machinery-related incidents within a year.
4. How do you handle employees who repeatedly violate safety policies?
- Answer: First, I ensure they understand the importance of safety policies through education. If violations continue, I implement a step-disciplinary process while keeping communication open and constructive. It’s about balancing firm enforcement with supportive guidance.
5. What is your approach to conducting a safety audit?
- Answer: My approach includes a comprehensive review of the workplace, interviews with employees, and analysis of safety data. I focus on identifying both compliance issues and opportunities for safety improvements, followed by a detailed report with recommendations.
6. How do you ensure safety during a major organizational change, like a merger or technology upgrade?
- Answer: I prioritize communication, involving everyone affected by the change. It’s crucial to assess the risks associated with the change and plan accordingly. Regular training and feedback sessions help in smoothly integrating safety into the transition.
7. What role does mental health play in industrial safety, and how do you address it?
- Answer: Mental health is vital for ensuring overall safety. Stress, fatigue, and other mental health issues can significantly impair judgment and reaction times. I advocate for mental health support programs and ensure that employees feel comfortable seeking help.
8. Can you explain how you would handle a serious on-site accident?
- Answer: Immediate response involves securing the area and providing necessary medical attention. I would then notify relevant authorities and conduct a thorough investigation to determine the cause. Addressing any systemic issues and learning from the incident is crucial for future prevention.
9. How do you engage employees in safety initiatives?
- Answer: Engagement comes from involving employees in safety discussions, encouraging them to share ideas, and recognizing their contributions to safety. Interactive training sessions and safety drills also help in keeping them actively involved.
10. What is your experience with environmental safety and how does it intersect with industrial safety?
- Answer: Environmental safety is integral to industrial safety. My experience includes managing waste disposal, controlling emissions, and ensuring the safe handling of hazardous materials. Both areas are interconnected, as a lapse in environmental safety can lead to workplace hazards.
Operational and Situational Questions
1. How would you assess and improve the safety of a new worksite you’re assigned to?
- Answer: I start with a thorough risk assessment, examining current safety protocols, employee practices, and potential hazards. Based on this, I prioritize areas needing immediate attention and develop a plan to address them, ensuring alignment with industry standards and regulations.
2. Describe a situation where you had to deal with an emergency at the workplace.
- Answer: In my last role, there was a chemical spill in the plant. I immediately activated the emergency response plan, which included evacuating the area, containing the spill, and coordinating with the hazardous materials team. Post-incident, I led a debrief to identify improvements for future response strategies.
3. What steps do you take if you notice a piece of machinery that is potentially hazardous?
- Answer: I would first put a temporary halt on its use and then conduct a detailed inspection in accordance with safety guidelines. If necessary, I’d recommend repairs or replacement, and ensure all staff are retrained on its safe operation.
4. How do you keep your team updated with the latest safety regulations and practices?
- Answer: Regular training sessions, safety meetings, and updates via emails or bulletins are key. I also encourage an open dialogue for any safety concerns or suggestions, fostering a proactive safety culture.
5. Describe how you would implement a new safety policy across a large organization.
- Answer: Implementation starts with clear communication of the policy’s purpose and benefits. I would organize training sessions, ensure accessible resources, and set up a timeline for the rollout. Monitoring compliance and gathering feedback are also crucial for a successful implementation.
6. Can you give an example of how you’ve reduced workplace accidents in your previous role?
- Answer: At my previous job, we had recurrent slips and falls. I initiated a ‘Zero Slip’ campaign focusing on proper footwear and floor safety. We also enhanced lighting and signage. Over six months, we saw a 60% reduction in such incidents.
7. How do you handle a situation where an employee is resistant to following safety procedures?
- Answer: I approach this with a mix of firmness and understanding. I’d discuss the reasons behind their resistance, educate them on the risks involved, and reiterate the importance of safety procedures. If non-compliance persists, I’d follow the company’s disciplinary protocols.
8. Explain how you would conduct a safety audit in a high-risk facility.
- Answer: A safety audit in a high-risk facility involves a comprehensive review of all operational areas. I focus on hazard identification, evaluating safety compliance, interviewing employees, and reviewing incident records. Following the audit, I provide a detailed report with actionable recommendations.
9. How do you ensure that safety equipment is used correctly by the staff?
- Answer: Regular training and demonstrations are key. I also conduct periodic checks and provide refreshers on the correct usage of safety equipment. Encouraging a culture where employees feel responsible for their own and their colleagues’ safety is also crucial.
10. What’s your approach to managing safety in a workplace with diverse operations and multiple hazards?
- Answer: Managing safety in such an environment requires a multi-faceted approach. I prioritize hazards based on risk level, ensure tailored safety protocols for different operations, and maintain clear communication channels for safety concerns. Regular reviews and updates of safety practices are also essential to cater to the evolving nature of operations.
Behavioural Questions
1. Describe a time when you had to advocate for safety improvements to senior management.
- Answer: At my previous job, I noticed recurring near-misses due to outdated equipment. I compiled incident reports, current research, and a cost-benefit analysis for upgrading the equipment. My presentation to senior management highlighted the long-term savings and safety improvements. As a result, they approved the investment.
2. Tell us about a difficult decision you had to make regarding safety in the workplace.
- Answer: Once, I had to decide whether to halt production due to a potential gas leak. I chose to stop operations and initiate an evacuation. Although it was a costly decision, the subsequent investigation revealed a significant leak, affirming that the safety of the workforce was paramount.
3. How have you dealt with an employee or a team reluctant to follow safety guidelines?
- Answer: I encountered a team resistant to new PPE guidelines. I organized an interactive workshop that illustrated the risks of non-compliance through real-life scenarios and interactive demonstrations. This approach helped them understand the importance and led to better adherence.
4. Can you give an example of how you handled a safety violation by a high-performing employee?
- Answer: A top performer was repeatedly bypassing a safety protocol to save time. I addressed it directly with the employee, emphasizing the importance of safety over speed. I also used this as a learning opportunity to reinforce the safety culture with the entire team.
5. Describe a time when you successfully managed a safety crisis.
- Answer: A major electrical fault occurred in the facility, posing a fire risk. I immediately initiated the emergency response plan, which included evacuation and contacting emergency services. My calm management during the crisis ensured no injuries and minimal disruption.
6. How do you handle feedback or criticism about your safety protocols?
- Answer: I welcome feedback as it provides a fresh perspective. For instance, when an employee suggested a more efficient way to conduct safety drills, I evaluated the idea, found it viable, and implemented it, which improved our safety drill process.
7. Share an experience where you had to adapt quickly to a change in safety regulations.
- Answer: When OSHA updated its regulations around hazardous materials, I had to swiftly adapt our protocols. I organized a series of training sessions and updated our compliance manuals. This proactive approach ensured a smooth transition with no compliance issues.
8. Describe how you maintain your own professional development in the field of industrial safety.
- Answer: I regularly attend industry conferences, participate in webinars, and engage with professional safety networks. Recently, I completed a certification in risk management, which has enhanced my skills in conducting thorough risk assessments.
9. How do you motivate others to maintain high safety standards?
- Answer: I believe in leading by example and recognizing good safety practices. I frequently share success stories of how adherence to safety protocols prevented incidents, and I recognize teams or individuals who consistently maintain high safety standards.
10. Can you talk about a time when you had to enforce safety protocols under tight deadlines or high pressure?
- Answer: In a project with a tight deadline, there was pressure to cut corners on safety. I insisted on adhering to all safety protocols, even under time constraints. I reorganized the team’s workflow to maintain safety standards without compromising the deadline.
Conclusion
As we wrap up our exploration of industrial safety interview questions, remember, these aren’t just queries to be answered; they’re opportunities for you to demonstrate your readiness to enhance workplace safety. As you walk into your interview, view each response as a platform to showcase your expertise and dedication to creating a safer environment. Armed with this newfound knowledge and self-assurance, step forward and make your mark, confidently tackling the demands of industrial safety.